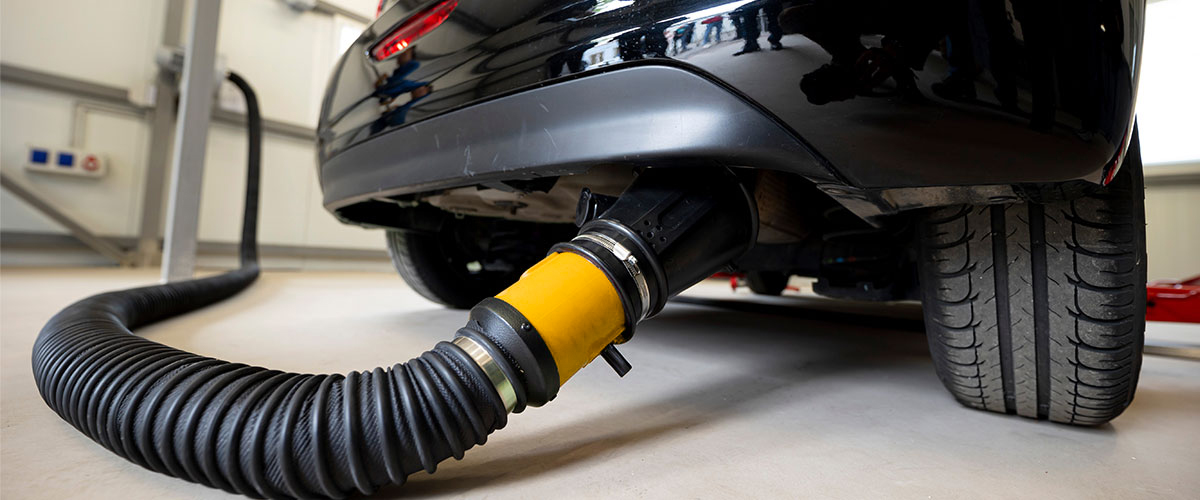
Recently, the automotive industry has been facing a number of hurdles that are adversely affecting its operations. The coronavirus pandemic, and the ongoing war in Ukraine, have hit the condition of car manufacturing companies and their components hard. An additional factor forcing drastic changes within the automotive industry, especially in exhaust gas after-treatment systems, is the increasingly stringent requirements imposed by the European Union in its legislative process, which aims to achieve total carbon neutrality by 2050. This is forcing the manufacturers of vehicles and their components to continuously reduce their exhaust gas and particulate emissions, a direct consequence of the need to introduce the Euro 7 standard.
According to the draft presented by the European Commission, the Euro 7 standard will be introduced.
According to a draft presented by a European Union committee, the new Euro 7 emission standard could take effect from 1 July 2025 (for cars and vans) and for trucks and buses from 1 July 2027. However, it is uncertain whether the above deadlines will be upheld, as the revolutionary legislation has not yet been enacted.
The latest guidelines stipulate:
- reduction of nitrogen oxide for cars (regardless of engine type) by 35% and by 56% for lorries and buses compared to the Euro 6 standard.
- reduction of particulate matter emissions by 13% (cars and vans) and by 39% for trucks and buses.
- imposing mandatory monitoring of exhaust emissions for 10 years or every 200 000 km.
Revolutionary in the new standard is the regulation of particulate emissions from tyres and brake pads (up to 7 mg/km, later even down to 3 mg/km).
The new standard also includes a change to the requirements for the monitoring of exhaust emissions.
Additionally, the changes also apply to batteries, which have to be more durable and efficient.
All of the above-mentioned changes are also applicable to batteries.
All the above-mentioned points will bring us to one conclusion – in the near future, we are facing further increases in car prices and possible problems with production efficiency, if the new standard requires specialised technical solutions and the use of rare materials for the production of, among others, particulate filters DPF/FAP.
How will Euro 7 affect the aftertreatment systems industry? Will it be able to meet the stricter standards?”
Unquestionably, further restrictions to limit the production of CO2, NOx and PM (fine particles free-floating in the air) present new challenges for aftertreatment system manufacturers and vehicle manufacturers themselves. This will probably involve the development of improved technology and the use of new components, which will ultimately translate into higher production costs and further price increases for end consumers.
What is currently the most effective form of regeneration for DPFs and catalytic reactors?
Currently, the most effective way of regenerating DPFs is the hydrodynamic method, carried out after disassembly of the element, in a specialised machine which, by means of strokes of water with detergent and air under high pressure, removes soot, ash, heavy metals, cerium oxides and other products of incomplete fuel combustion that are deposited in the channels of the monolith. Importantly, after the regeneration process, the filter undergoes thorough drying. As a result, the element, after comprehensive regeneration, safely regains its factory properties confirmed by a back pressure test before and after cleaning. The best protection of the filter and the certainty of failure-free driving will be provided by the application of preventive regeneration of the DPF, at intervals depending on the kilometres driven and the type of vehicle.
In addition to the revitalisation of the DPF, it is also necessary to ensure that the filter is not damaged.
In addition to the sensational results provided by water cleaning, this method has another very important advantage – it is cheap and environmentally friendly, because it allows to reuse the refurbished monolith and reduces the production of new components.
Will the announced changes related to the Euro 7 standard affect the technology of regeneration/cleaning of DPFs, SCR catalysts?
Whether the Euro 7 standard will affect the technology used in DPF and catalytic converter regeneration equipment depends mainly on the car manufacturers, as well as the evolution of the parts used in new vehicles. Only when it becomes possible to carry out tests on the new generation of filters will it be possible to determine whether the current methods of cleaning exhaust aftertreatment systems will stand up to the new developments. As the market leader in DPF regeneration machines, we are very likely to assume that the evolution of our equipment may be necessary to adapt it to work with even more sophisticated aftertreatment systems.
Our team is a group of capable and ambitious specialists who strive for continuous improvement of the equipment we produce, modification of the technology for Euro 7 filters is only a matter of time. It may also turn out that changes in equipment design will not be necessary. We look forward to testing the new filter systems.